Для того, чтобы изготовить качественную деталь необходимо выполнить два условия:
1. Разрабатываемый технологический процесс должен обеспечивать изготовление детали с необходимой точностью размеров, формы, расположения поверхностей и качеством поверхностного слоя.
Только в этом случае деталь будет обладать необходимыми эксплуатационными свойствами, что позволит ей выполнять свое служебное назначение.
2. Для того чтобы деталь могла выполнить свое служебное назначение в станке, она должна быть получена в строгом соответствии с технологическим процессом ее изготовления.
Рассмотрим последовательность разработки технологического процесса:
1. Критический анализ исходной информации.
2. Выбор заготовки и рационального метода её получения.
3. Выбор технологических баз.
4. Определение последовательности и содержания технологических операций.
5. Выбор средств технологического оснащения.
6. Расчёт режимов резания.
Рассмотрим подробно каждый из этих этапов.
Первый этап.
На первом этапе технолог проводит критический анализ исходной информации: по конструкторской документации он уточняет служебное назначение детали в станке; материал, из которого она должна быть изготовлена; конструкторские базы; требования к точности и качеству поверхностного слоя (здесь необходимо уточнить заложенные в КД требования к точности и качеству поверхностей детали с учетом технических и экономических факторов производства).
К сожалению, немногие технологи уделяют должное внимание этому этапу. Основная масса технологов берет за основу типовой технологический процесс (не путать с групповым), на его основе разрабатывает рабочий техпроцесс, не утруждая себя творческой переработкой имеющейся информации и тем самым лишая себя творческого роста, а предприятие – увеличения прибыли и повышения технического уровня производства и, как следствие этого, повышения зарплаты.
В чем же будет заключаться критический анализ для нашего конкретного случая – вала? (рис. 3.3).
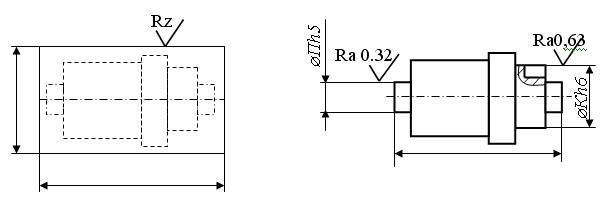
Точность шеек вала под подшипники, обозначенные на эскизе øПh5, соответствует пятому квалитету; шероховатость поверхности – девятому классу шероховатости. Для выполнения этих требований КД технолог будет вынужден в качестве финишной операции использовать тонкое шлифование.
Грамотный специалист критически отнесется к этой информации и попробует, исходя из служебного назначения вала в сборочной единице и возможностей действующего производства, расширить поле допуска до h6 и увеличить шероховатость до Ra 0,8.
Точность цилиндрической поверхности øКh6 соответствует шестому квалитету, а ее шероховатость – восьмому классу шероховатости (согласно ГОСТ 2789-73). И в этом случае технологу следует рассмотреть возможность расширения поля допуска до h7 и увеличения шероховатости до Ra 1,25 мкм.
В общем случае логическая структурная схема критического анализа представлена на рис. 1, к которой следует добавить следующее: особенно критичны будьте с конструкторской информацией во время отработки конструкции детали на технологичность.
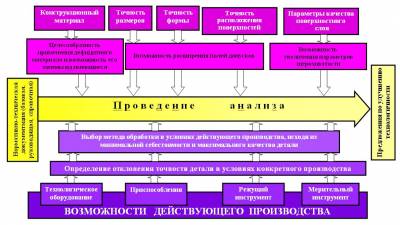
Рис. 1. Структурная схема критического анализа.
Второй этап.
На втором этапе разработки технологического процесса необходимо выбрать заготовку, исходя из следующих предпосылок:
1. Минимальная себестоимость детали.
2. Минимальная себестоимость заготовки.
Точные методы получения заготовок (штамповка вместо ковки; литье в многократные формы вместо литья в разовые формы и др.) оправдывают себя в крупносерийном и серийном производстве, где себестоимость детали будет минимальна. В мелкосерийном производстве для получения заготовок используют резку из сортового, фасонного и листового проката; литье в песчаные формы; ковку.
В любом случае, при выборе оптимального варианта получения заготовок необходимо учитывать, какое влияние он оказывает на себестоимость последующих методов обработки. Бывает, что даже в мелкосерийном производстве предпочтительнее перейти на более точные и производительные способы получения заготовок, т. к. более дорогая заготовка, изготовленная с меньшими припусками и с большей точностью, может оказаться в итоге выгоднее дешевой заготовки.
Это связано с тем, что ряд способов получения заготовок (литье под давлением, штамповка на механических прессах) позволяет снизить трудоемкость последующей механообработки и сборки, что приводит к снижению общей себестоимости (затраты – З) и повышению эффективности производства (Э=Р/З).
Третий этап.
Третий этап разработки технологического процесса – выбор технологических баз (рис. 2).
Существуют различные способы базирования. Они достаточно полно и подробно рассмотрены в соответствующих учебниках.
Для нашего случая мы выберем классическую схему базирования для валов: двойная направляющая и двойная опорная базы (обработка в центрах).
Четвёртый этап.
Четвертый этап – определение последовательности и содержания технологических операций основан на знаниях технологических методов и видов обработки, а также используемых в них режущих инструментов.
В нашем конкретном случае мы выбрали (рис. 2):
Рис. 2. 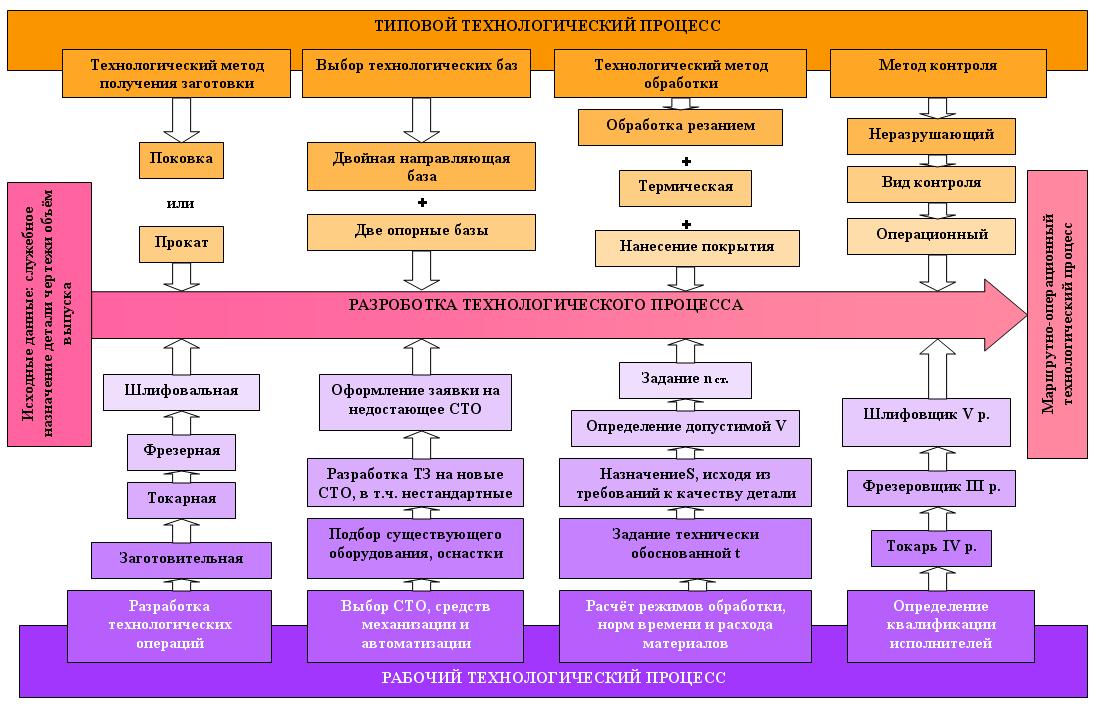
- для получения цилиндрических и торцовых поверхностей, а также шпоночного паза обработку резанием;
- для увеличения твёрдости посадочных поверхностей под подшипники и шпонку - термическую обработку шеек вала и поверхностей шпоночного паза;
- для увеличения коррозионостойкости поверхностей - нанесение покрытия.
Для получения детали в соответствии с чертежом были выбраны следующие виды лезвийной обработки:
- точение;
- фрезерование;
- шлифование.
Соответственно операции :
– токарная;
- фрезерная;
- шлифовальная – по ГОСТ 3.1702-79.
Пятый этап.
На пятом этапе при выборе СТО остановились на стандартном оборудовании, стандартных приспособлениях и стандартном режущем и мерительном инструменте (см. рис. 3).
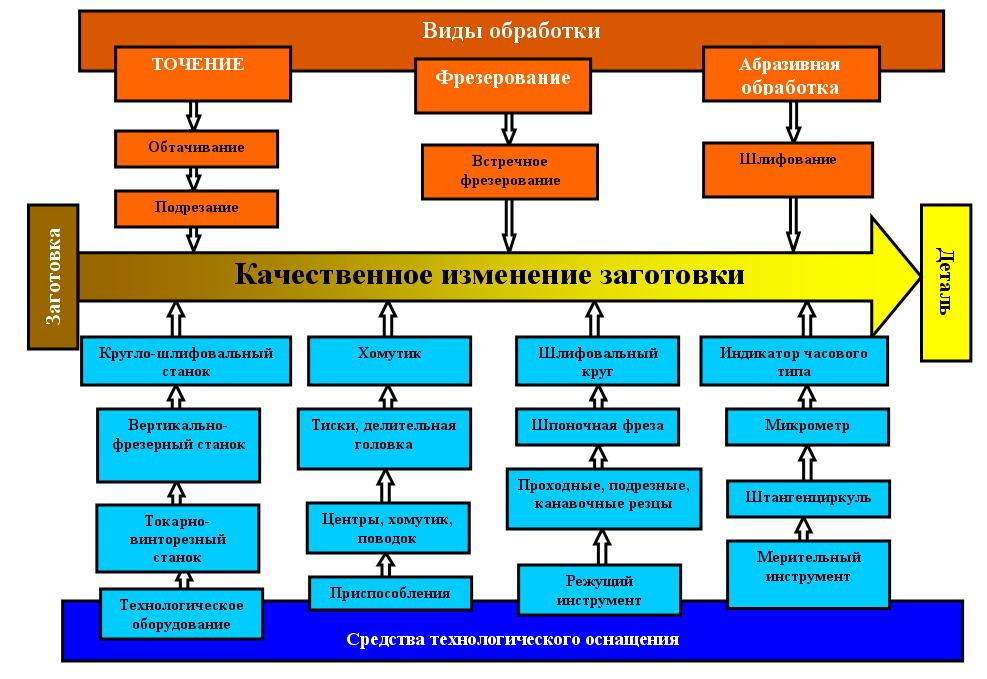
Рис. 3. ЛСС техпроцесса изготовления вала.
Шестой этап.
Очень важен шестой этап – назначение и расчет режимов обработки (режимов резания).
Режим резания – совокупность значений скорости резания – V, подачи – s и глубины резания – t.
Режим резания оказывает влияние на целый ряд производственных показателей, основными среди которых являются точность, технологичность эффективность. Поэтому очень важно в совершенстве владеть методикой расчета режимов резания.
Расчет режимов резания сводится к определению рациональных параметров обработки, главное назначение которых – получение качественной детали (рис. 4).
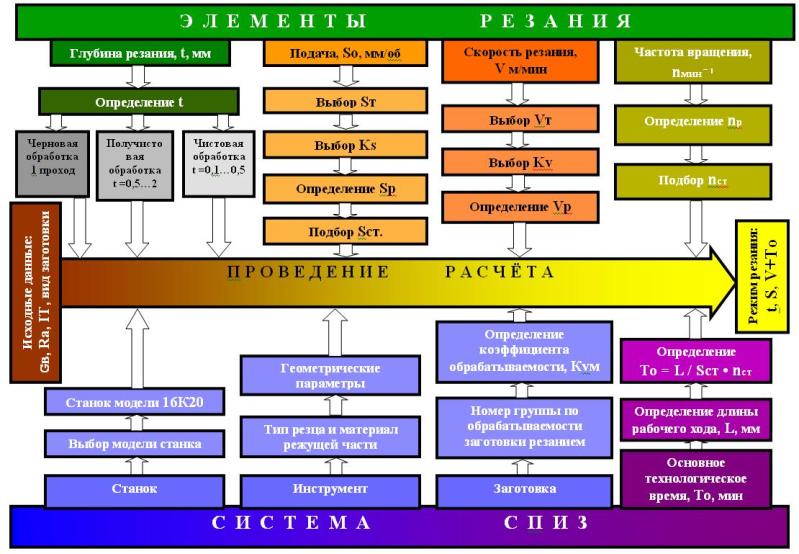
Рис. 4. ЛСС расчёта режима резания.
Эта рациональность заключается в оптимальном сочетании элементов резания (t,s,n,V) с параметрами системы СПИЗ (модель и состояние станка, геометрические параметры инструмента, физико-механические свойства заготовки и инструментального материала).
Расчет начинают с анализа исходных данных, основными среди которых являются: обрабатываемый материал (марка, предел прочности, твердость); вид заготовки (поковка, штамповка, отливка, пруток, предварительно обработана); точность размеров и шероховатость обработанных поверхностей. Затем продолжают расчет в следующей последовательности:
1. Выбор модели станка с учётом жесткости технологической системы.
2. Определение номера группы заготовки по обрабатываемости резанием.
3. Выбор типа резца, конструкции лезвия и направления подачи, материала режущей части, геометрических параметров.
4. Определение глубины резания t.
5. Выбор табличного значения подачи Sт., определение расчетного значения подачи. Задание Sст (по паспорту станка).
6. Выбор табличного значения скорости резания Vт. Определение расчетного значения Vр.
7. Определение расчетного значения частоты вращения шпинделя nр. Задание nст (по паспорту станка).
8. Определение основного технологического времени, То, которое является показателем производительности обработки. При черновой обработке стремятся к минимальному значению То.
Ещё раз отметим, что от правильного выбора режима резания зависит качество детали , период стойкости режущего инструмента (рис. 5) и износ станка.
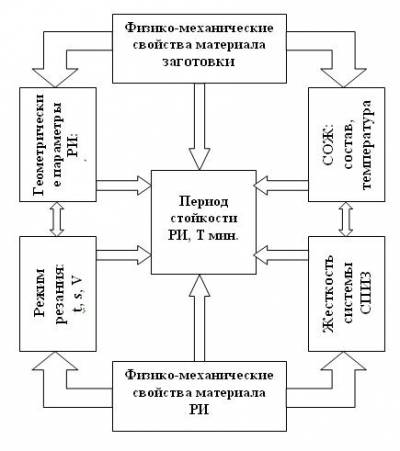
Рис. 5. Зависимость стойкости режущего инструмента от различных факторов.
|